Pickleball has become a popular and fashionable sport for leisure. It combines elements of tennis, badminton and table tennis, which can be called a “hybrid”. In the next ten years, some institutions predict that the pickleball market will reach 4 billion US dollars, of which the racket accounted for 12% of the market share. The majority of pickleball rackets use composite materials, which gives the product an exciting boost, and the composite industry is very concerned about this.
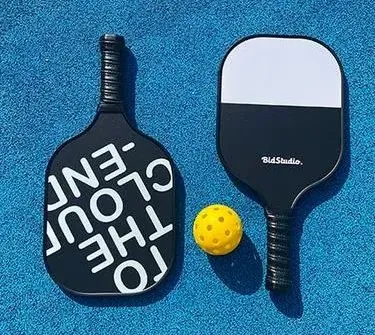
Composite Pickleball rackets Today, most pickleball rackets have a polymer core and a fiberglass panel. The core is made of thermoplastic polymer honeycomb material and is produced through a continuous on-line manufacturing process. Many manufacturers cover the core material with a nonwoven polyethylene terephthalate (PET) layer to enhance the bonding surface area (as shown in Figure 2). Fiberglass panels are applied to core materials through a variety of different processes and stacking sequences, and many manufacturers are beginning to differentiate at this stage.
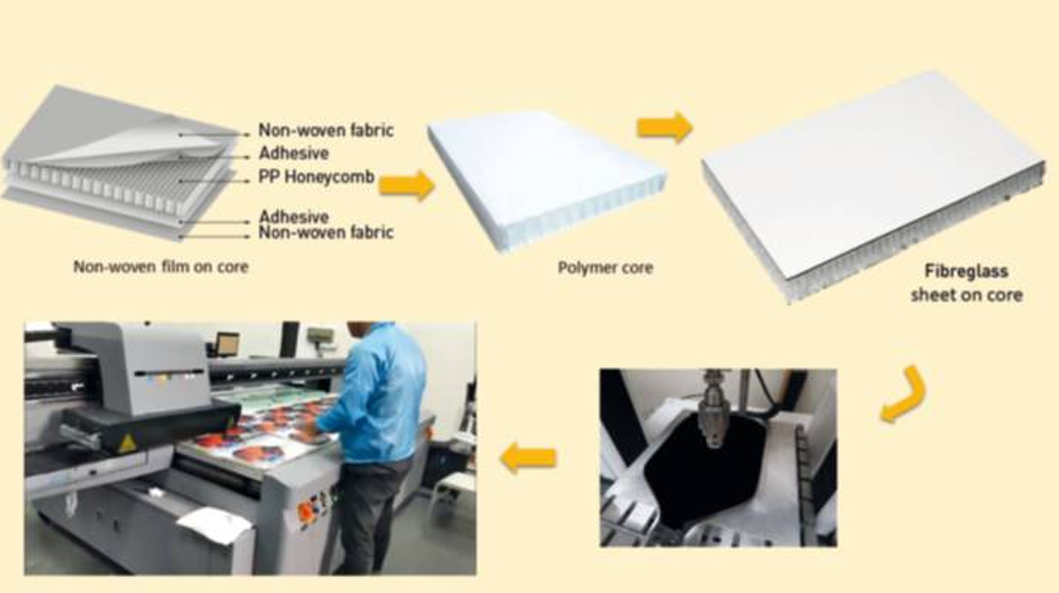
In general, the most commonly produced rackets are made of 0/90 woven high-yarn fiberglass gauze, which is laid on the surface of the mold and impregnated with polyester resin. The choice of resin has a significant impact on the responsiveness (bounce sensation) and power of the racket. After curing, these panels are bonded with a compatible resin, usually thixotropic to prevent resin flow and reduce voids. Manufacturers often add additives to increase the viscosity of the resin for a better bonding effect.