At present, the low-altitude economy is accelerating, and the weight reduction of aircraft has become a focus of attention.
Carbon fiber material is the key track of aircraft lightweight, carbon fiber material with light and strong, high strength, high elasticity and high temperature resistance and other characteristics, is expected to become the core growth point of low-altitude economic upstream materials.
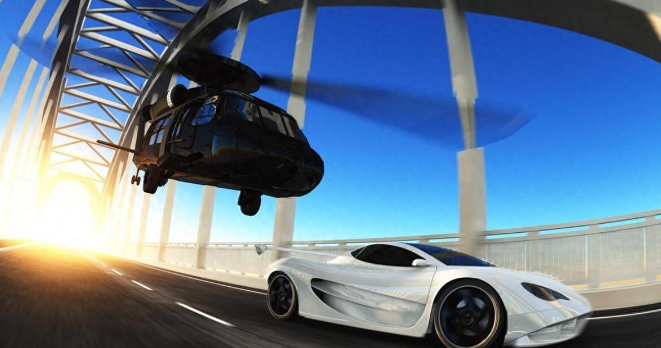
Carbon fiber is known as the “king of new materials”, its manufacturing process is unique and precise, in the 1000-3000°C high temperature inert gas environment, from organic fibers such as polyacrylonitrile (PAN), asphalt or viscose conversion, its diameter between 5-10 microns, carbon content of up to 90%.
After cracking and carbonization, carbon backbone structure is formed.
This inorganic polymer fiber with a carbon content of more than 90% is one of the lightest inorganic materials available.
Carbon fiber is widely used in many fields such as aerospace, military, energy, sporting goods, automobiles and building reinforcement.
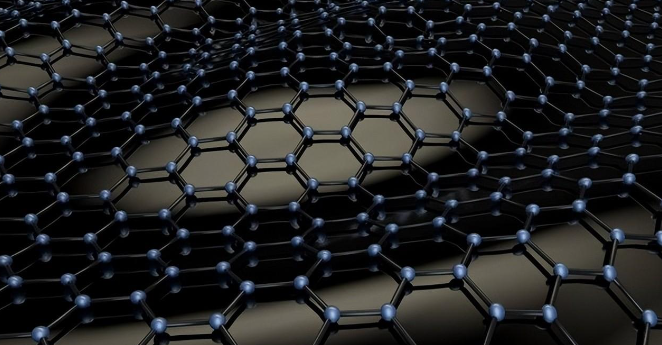
As a single brittle material, carbon fiber has a limited use case, but it plays an important role in composite materials.
Composite material is a new type of material obtained by two or more kinds of materials through a specific composite process, which not only retains the main characteristics of the original component, but also obtains the special properties that the original component cannot match through the synergistic effect.
Carbon fiber is an important subdivision of composite materials, generally in the form of resin carbon fiber, in the role of reinforcement in composite materials. With carbon fiber as the reinforcement material, combined with carbon or silicon carbide matrix, through chemical vapor deposition or liquid phase impregnation and other processes, a variety of composite materials can be formed, such as carbon/carbon composite materials, carbon/ceramic composite materials.
Parts made of carbon fiber composite materials are only 15%-30% of the weight of traditional aluminum alloy materials, which has significant lightweight advantages. Carbon fiber braid, carbon fiber prepreg, carbon fiber pultrusion plate and other products can be formed through different processing methods.
Depending on the number of fibers, carbon fibers can be divided into large and small strands.
In general, carbon fibers with a number of strands less than 24K are called small strands, while those above 24K are large strands.
Because of its excellent performance, the small tow is mainly used in national defense, aerospace and other fields. The large tow is mainly used in the industrial field because of its lower cost.
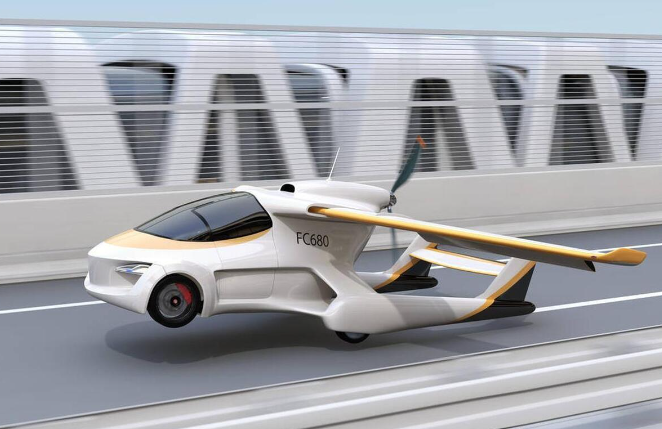
From the perspective of the industry chain, the carbon fiber industry chain includes the whole process from raw material extraction to final molding.
Upstream enterprises in the industrial chain extract propylene from petroleum, coal, natural gas and other fossil fuels, through ammoxidation reaction to obtain acrylonitrile, acrylonitrile is processed into polyacrylonitrile (PAN) precursor through polymerization and spinning process, which is a key precursor for the preparation of carbon fiber.
Manufacturers in the lower reaches of the industry chain take over the PAN filament and pre-oxidize it to transform it into a heat-resistant trapezoidal structure.
After low temperature carbonization and high temperature carbonization, PAN precursor is gradually transformed into carbon fiber with disorderly graphite structure.
In this process, the preparation of high-quality PAN filaments is a prerequisite for obtaining high-performance carbon fibers. In the process of carbon fiber preparation, oxidation furnace and carbonization furnace are the core equipment.
The oxidation furnace is used to convert the PAN filament into a heat-resistant trapezoidal structure, while the carbonization furnace is responsible for gradually removing non-carbon elements from the filament at high temperatures, and finally obtaining high-performance carbon fibers with a carbon content of more than 99%.
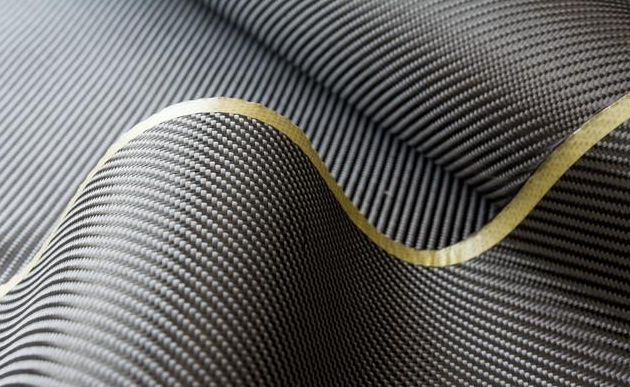