Composite sandwich structure promotes the design and application of lightweight composite materials. Because composite sandwich structure has the advantages of light weight, high strength, heat insulation and wave absorption, it is widely used in aerospace, automobile and other major engineering fields. The rigid panel of the sandwich structure is far away from the neutral axis under the support of the lightweight core layer, which greatly improves the cross-section moment of inertia of the structure and improves the overall mechanical performance of the structure.
However, how to ensure the reliable connection between the panel and the core layer and then play the advantages of the overall performance of the sandwich structure is the focus of academia and industry for a long time
Sandwich structure is composed of high strength panel and light core material. At present, the panel and core material of sandwich structure are widely used for heterogeneous materials, such as thermoset composite materials such as epoxy resin as panel, and light materials such as paper honeycomb and aluminum honeycomb as core material of sandwich structure. However, the surface and core interface strength of the panel and core material of dissimilar materials is low, and the panel and core material are difficult to be recycled. The sandwich structure of thermoplastic composite material can take advantage of the characteristics of thermoplastic resin can be melted and reprocessed to complete the melting connection and form a reliable and stable surface core connection interface. Thermoplastic composite sandwich structure provides a new concept for the design and molding of composite lightweight structure, which is a lightweight and multifunctional structure widely used at present.
Sandwich structure design
In sandwich structure, the core material as the core can make the panel away from the neutral axis, maximize the bending performance of the structure, and at the same time, the core material supports the panel to prevent local buckling. According to the microstructure of sandwich structure, periodically ordered cell materials can be divided into two dimensional corrugated materials, two dimensional honeycomb materials and three dimensional lattice materials. The panel material and the core layer material of the sandwich structure have different effects on the overall performance of the structure, so the different configuration of the core material of the sandwich structure and the different design scheme of the panel material have different effects on the mechanical properties of the structure.
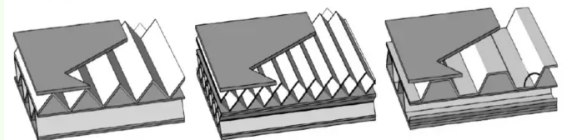

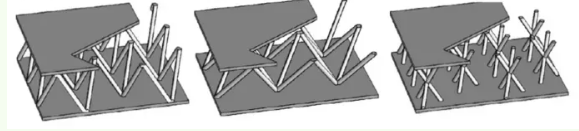
In the honeycomb sandwich structure, light honeycomb material as the core can improve the mechanical properties of the structure as a whole. Because of its reliable mechanical properties and excellent designability, it has been widely used in aerospace, vehicle, construction, machinery and other fields. Compared with traditional honeycomb structure, thermoplastic composite honeycomb structure has many advantages, such as high specific strength, high specific stiffness, excellent fatigue resistance, corrosion resistance and high temperature resistance. So in recent years, fiber reinforced thermoplastic composite honeycomb sandwich structure is gradually replacing the traditional aluminum honeycomb and paper honeycomb with its excellent performance of lightweight. Honeycomb materials are an important class of porous materials, mainly two-dimensional polygonal arrays, which reduce excess weight while retaining the main bearing capacity of the structure. With the continuous progress and development of honeycomb manufacturing technology, honeycomb structure can be composed of metal, non-metal, paper, polymer and other forms.
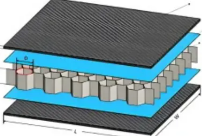
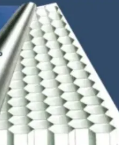
With high specific stiffness, high specific strength, high designability, and multifunctional integration potential, fiber reinforced composite sandwich structures with lattice structure are attractive in the construction of lightweight, multifunctional structures, especially in aerospace and Marine systems. With the development of composite materials, the preparation technology of composite lattice sandwich structure is also developing rapidly.
Material of sandwich structure
The materials used in sandwich structure are mainly divided into two types of materials: panel and core material. The panel and core material of traditional sandwich structure use different materials, so the strength of the connection interface between panel and core material is not high. Because the panel and core material of the sandwich structure of thermoplastic composite material are selected thermoplastic composite material, no new material is introduced, and a stable and reliable surface core connection interface can be obtained. The panel material of thermoplastic composite sandwich structure is generally made of reinforced fiber and thermoplastic resin, and the core material is generally made of pure thermoplastic resin.
The panel material of thermoplastic composite sandwich structure is generally composed of fiber reinforced thermoplastic composite laminate, and the reinforced fiber uses short fiber or continuous fiber. Sandwich structure panels can be semi-prepreg or prepreg. Thermoplastic matrix polymers can generally be selected as engineering plastics such as polypropylene (PP) or polyamide (PA) or high-performance polymers such as polyether imide (PEI) and polyether ether ketone (PEEK). Commercial plastics are usually used in combination with reinforced glass fibers, especially PP-based composites. The most widely used high-performance polymer for thermoplastic composite sandwich panels in the aerospace industry is polyetherimide (PEI), which is usually used in combination with reinforced glass fiber.
Thermoplastic composite core material density is usually lower than skin material, according to their structure can be divided into three categories: corrugated core or truss core, foam core or solid core, honeycomb core with hexagonal element, round element or square element. The common core layer materials are balsa, Nomex honeycomb, polyurethane (PUR) foam, polyvinyl chloride (PVC) foam, and aluminum honeycomb. Currently the most commonly used are thermoplastic foam or honeycomb cores, both of which are completed by different kinds of thermoplastic polymers such as PP or PEI.
Sandwich structure preparation and forming process
The panel design and core configuration design of the sandwich structure have certain influence on the overall mechanical properties of the sandwich structure. The panel of the sandwich structure will affect the bending performance of the structure, and the core material will affect the bending performance and flattening performance of the sandwich structure. In addition, the connection between the panel and the core material of the sandwich structure will affect the interface performance of the face core, and then affect the peel strength of the structure. Therefore, the preparation process of sandwich structure and the preparation process of panel will affect the performance of the overall structure.
The panel material of thermoplastic composite sandwich structure is generally fiber reinforced thermoplastic composite material, and the molding methods of fiber reinforced thermoplastic composite material mainly include hot pressing, injection molding, pultrusion molding, winding molding and stamping molding and other traditional molding methods. In addition to the traditional molding methods, there are automatic composite material preparation technology. For example, additive manufacturing technology (AM), fiber winding technology (FW), automatic belt laying technology (ATL), automatic wire laying technology (AFP).
Thermoplastic composites can be adapted to adhesives according to the types of materials to connect the panel and core material of composite sandwich structure, and achieve reliable connection between the surface and core. According to the characteristic that thermoplastic composites can be fused and reprocessed, the panel and core material of sandwich structure can be connected by means of melting connection. It mainly includes welding, hot pressing, bonding, 3D weaving and additive manufacturing. 3D weaving and additive manufacturing can realize the integrated molding and preparation of thermoplastic composite sandwich structure.
Composite sandwich structure is widely used in automotive, aerospace, architecture and other major engineering fields because of its high specific stiffness, specific strength and multi-function characteristics. The structure with specific requirements can be obtained through the design of sandwich structure. Thermoplastic composite sandwich structure can be recycled, and the panel and core material of thermoplastic composite sandwich structure use the same material, because no new material is introduced, the strength and performance of the surface core interface is better.