- The origin of carbon fiber
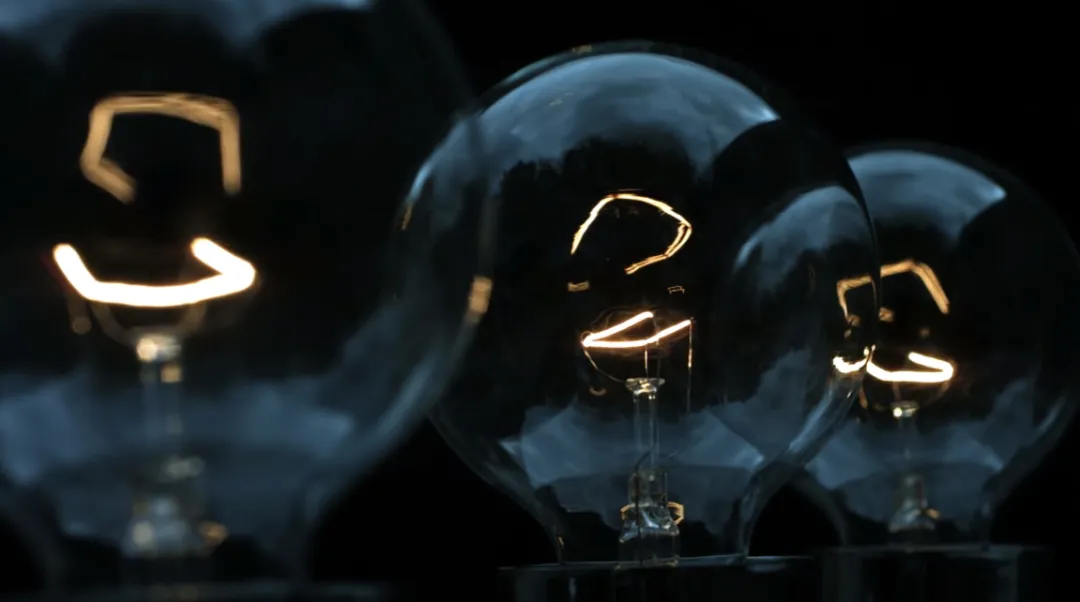
The history of carbon fiber dates back to 1860, when the British chemist Joseph Swan first used carbon fiber materials for semi-vacuum lamps. Until the 1960s, the advent of polyacrylonitrile-based carbon fibers with excellent physical properties and elastic modulus has really promoted carbon fibers into the commercial application stage of high-performance materials after a hundred years.
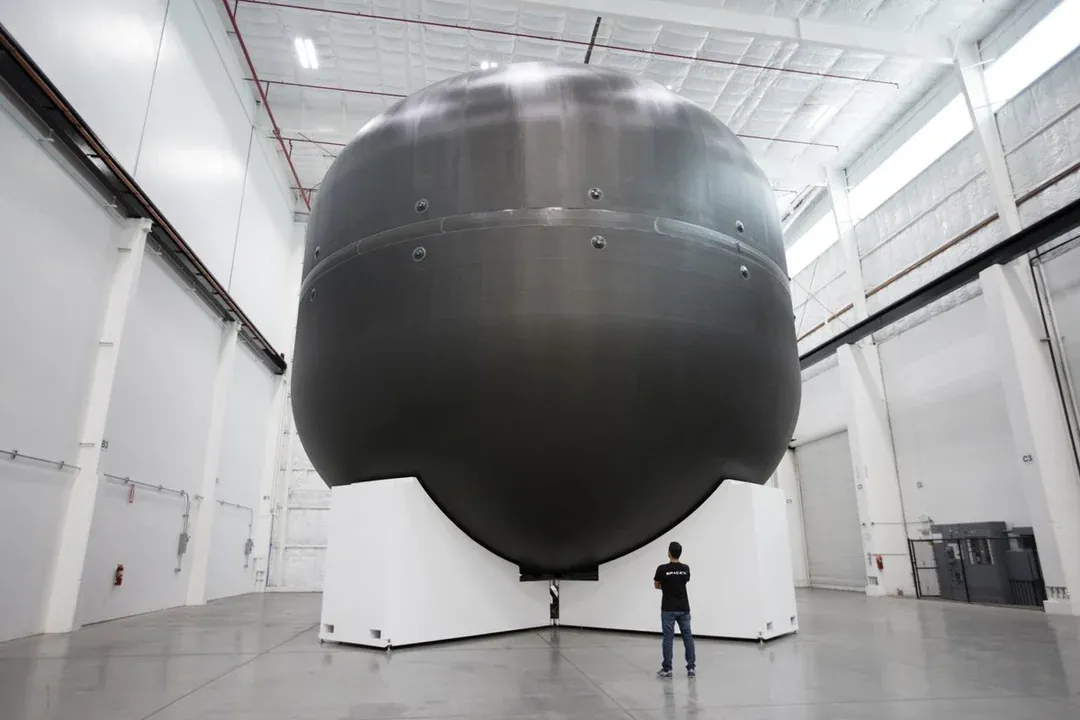
After carbon fiber entered the stage of rapid development, for a long time, due to its excellent performance and high production costs, it was once known as “black gold”, mainly used in the “luxury” field such as aerospace and high-end sports equipment, and the popularity is very poor.
In order to expand the application, carbon fiber manufacturers began to improve product performance to increase demand, while reducing costs to broaden the market. The cost reduction program is roughly divided into two directions: first, through the production of large tow carbon fiber products to reduce the investment in production equipment and process requirements; The second is to improve production efficiency, such as the use of dry spray wet spinning process to improve cost efficiency and performance. Industrial-grade large tow carbon fibers are now widely used in automotive, wind turbine blades, crystalline silicon melting furnaces and hydrogen storage tanks in the photovoltaic industry.
- Structure and properties of carbon fiber
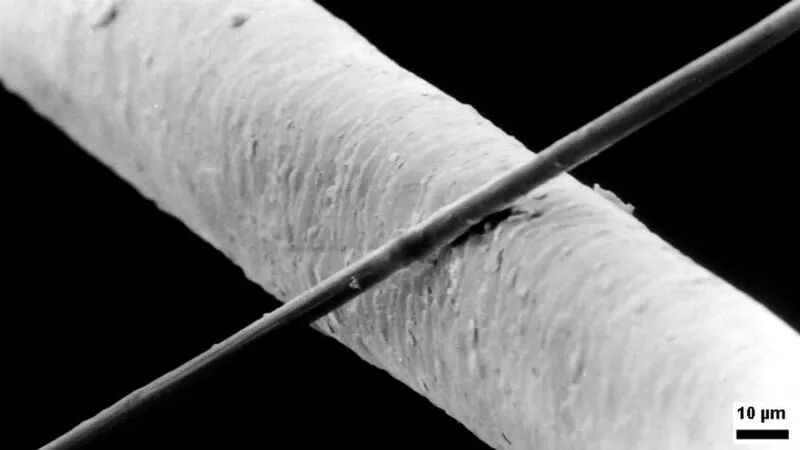
Carbon fiber is usually supplied in the form of continuous strands wrapped around a spool that can be easily untangled from the spool for use. Each bundle consists of thousands of smaller carbon fiber filaments, protected and held together by organic coatings or pastes such as polyethylene oxide or polyvinyl alcohol, each of which is a continuous cylinder with a diameter of 5-10 microns and composed almost entirely of carbon. The earliest carbon fiber products, such as T300, HTA, and AS4, were 16-22 microns in diameter. Later carbon fibers (such as IM6 or IM600) have a diameter of about 5 microns. The density of carbon fiber is generally 1750kg/m³.
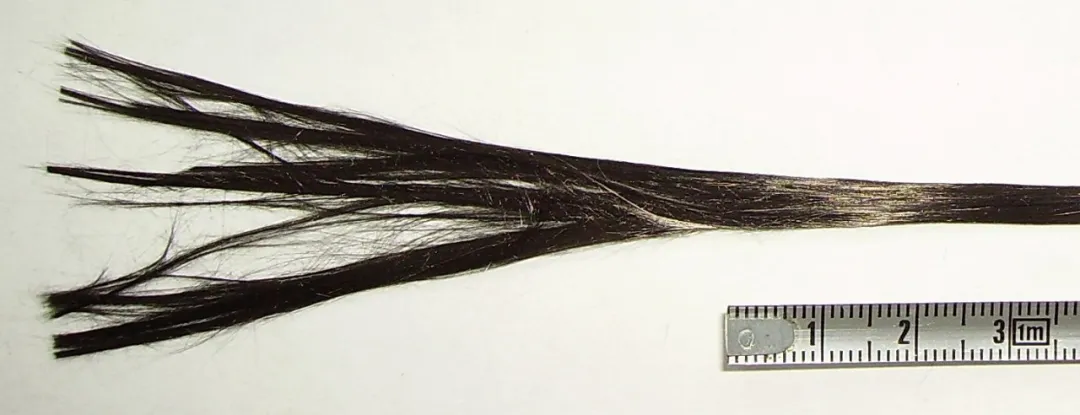
The atomic structure of carbon fiber is similar to that of graphite, consisting of sheets of carbon atoms arranged in a regular hexagonal pattern (graphene sheets), the difference between the two lies in the way the layers are connected to each other. Graphite is a crystalline material in which the sheets are stacked parallel to each other in a regular manner, whereas carbon fiber is not crystalline and the interlayer connections are irregular, which prevents slipping and gives the carbon fiber high ultimate tensile strength.
Carbon fiber has strong thermal conductivity and high temperature resistance, which can theoretically not melt at a high temperature of 2000 ° C, but carbon fiber is often not used alone and needs to be used together with materials with a relatively low melting point such as epoxy resin.
- Carbon fiber manufacturing process
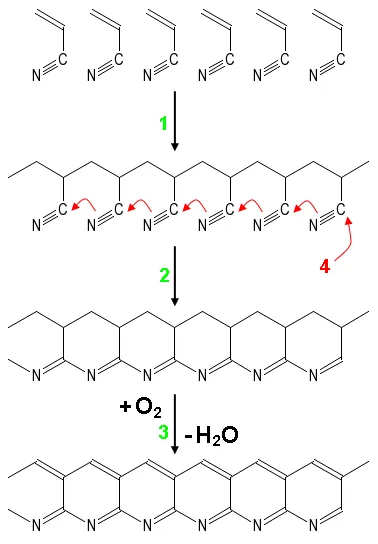
About 90% of the world’s carbon fiber is made from polyacrylonitrile (PAN), with the remaining 10% made from polymers such as rayon or petroleum asphalt. These polymers are all called precursors, and for synthetic polymers such as polyacrylonitrile or rayon, the precursors are first spun into filament yarns, using chemical and mechanical processes to initially arrange the polymer molecules to enhance the final physical properties of the finished carbon fiber. The precursor composition and mechanical process used by different manufacturers in spinning filament yarns may vary. After spinning, the polymer filament yarn is heated at a high temperature to remove carbon atoms (carbonization), thus making carbon fiber.
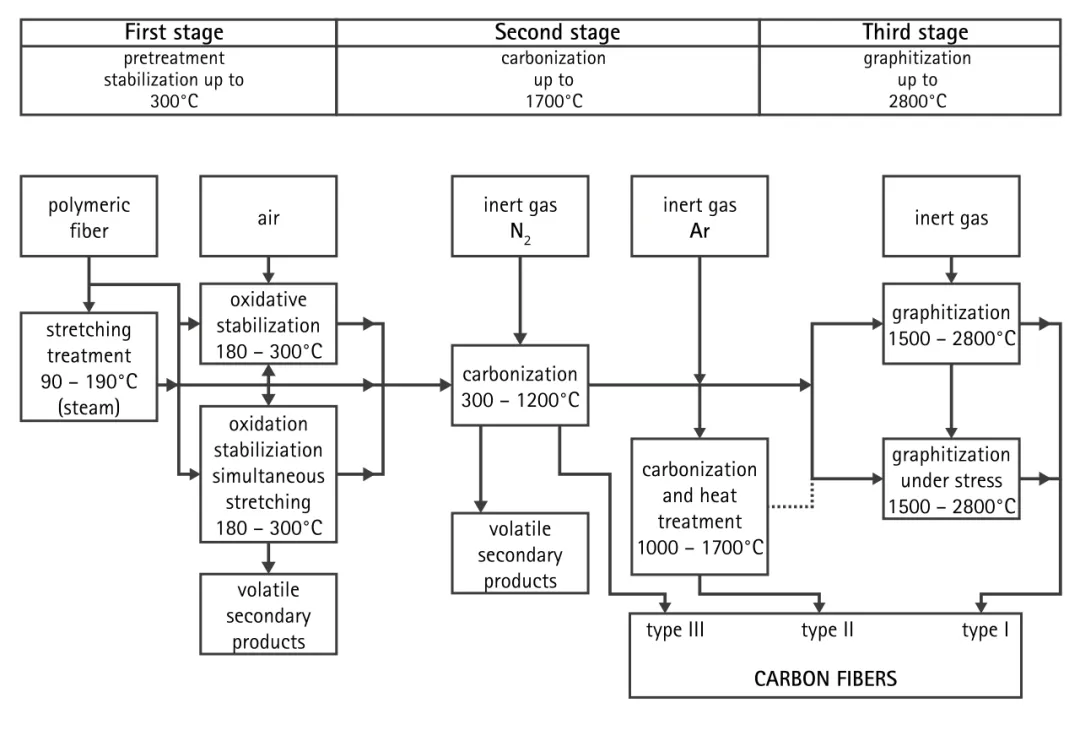
- Application of carbon fiber
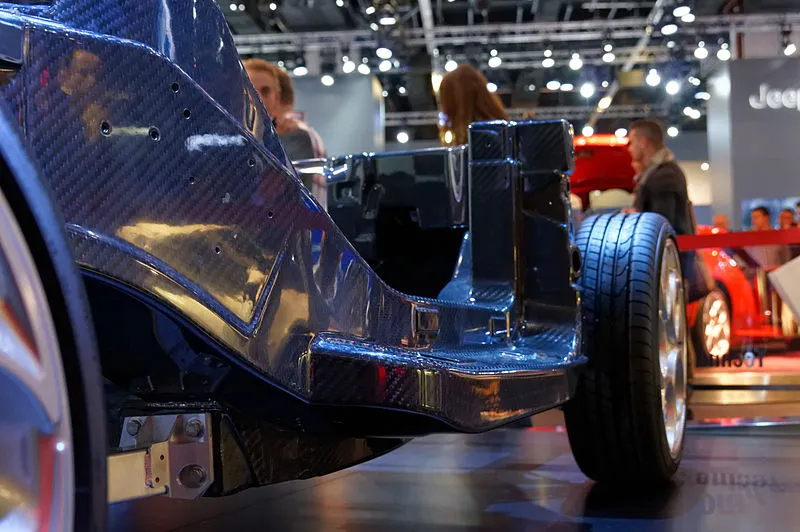
Because of its excellent physical properties, carbon fiber materials are often used in the manufacture of aircraft and aerospace components, racing car bodies, golf club bodies, bicycle frames, fishing rods, construction materials, automotive parts, sailing masts, and many other components that require light weight and high strength.
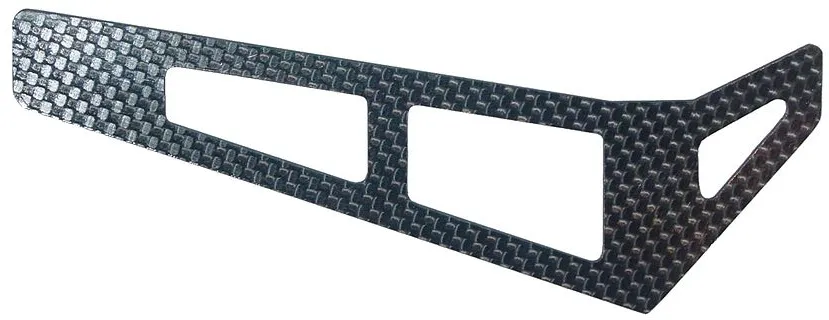
The most significant use of carbon fiber is to make reinforced composite materials, carbon fiber reinforced plastics because of its high strength, light weight characteristics, as well as high temperature resistance, radiation resistance, water resistance and corrosion resistance, become the ideal material for manufacturing aircraft, weapons and special working equipment.
However, carbon fiber materials are difficult to degrade naturally, and disposing of them in large quantities may cause environmental problems. In recent years, carbon fiber composite materials have been widely used in the manufacture of large aircraft, such as Airbus A350 and A380, Boeing 787 and other models, using carbon fiber composite materials to reduce the weight of the fuselage to reduce fuel consumption. In addition, the demand for carbon fiber composite materials for large wind turbine blades, racing cars, automobile bodies, and various sporting goods is also increasing.
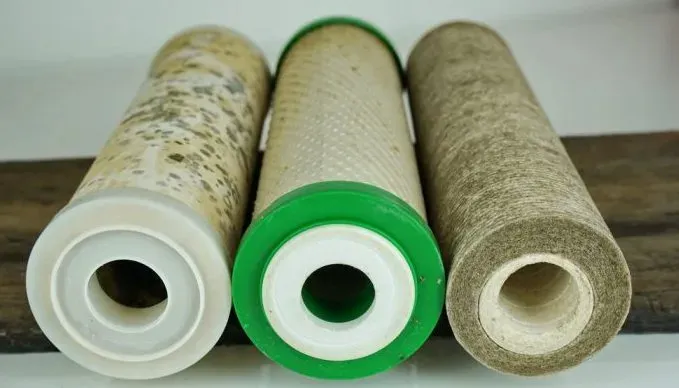
After carbon fiber is activated, it becomes “activated carbon fiber”. This activated carbon fiber material has a large number of micropores, forming nanospace and having a large specific surface area. With excellent adsorption and desorption ability, the most common product is the mask used in life, this material is also used in various filters or water purifiers.