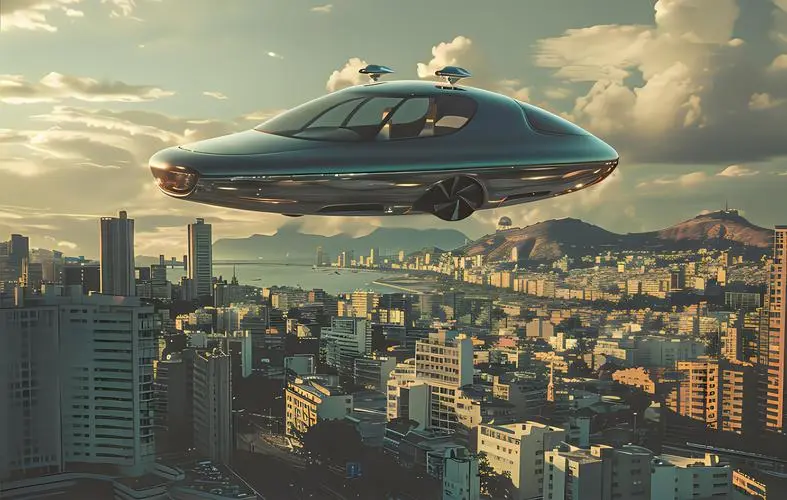
The year 2024 marks the starting point of China’s low-altitude economic industry, which covers a variety of aircraft such as drones, low-altitude aircraft, and air taxis, indicating that a huge industry is taking shape. With the rapid growth of low-altitude economy, it has brought innovative changes to many fields such as logistics, agriculture, emergency services, tourism, and also provides a new stage for the application of composite materials.
Because of its advantages of light weight, high strength, corrosion resistance and plasticity, composite materials have become ideal materials for manufacturing low-altitude aircraft. In this low-altitude economic era of efficiency, endurance and environmental protection, the use of composite materials not only affects the performance and safety of aircraft, but also the key to promoting the development of the entire industry.
From carbon fiber-reinforced drone wings to lightweight structures made of fiberglass, innovations in composite materials continue to power the growth of the low-altitude economy. The close connection between low-altitude economy and composite materials is reflected in technological progress and industrial upgrading. With the gradual relaxation of global policies in the low-altitude field, and the continuous emergence of new materials and processes, the application of composite materials in the field of low-altitude aircraft is facing unprecedented opportunities.
Let’s take a closer look at composites used in low-altitude aircraft.
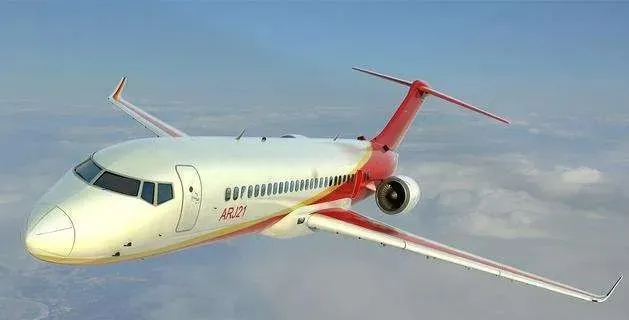
Carbon fiber composite
The rapid growth of low-altitude economy has not only brought innovative changes to many industries such as logistics, agriculture, emergency rescue, and tourism, but also provided a huge development space for the use of composite materials, especially carbon fiber.
Carbon fiber is an ideal material for low-altitude aircraft manufacturing because of its light weight, high strength and corrosion resistance. It can not only reduce the weight of the aircraft, but also improve performance and economic efficiency, becoming an effective alternative to traditional metal materials.
According to Stratview data cited by the China Composite Materials Industry Association, more than 90 percent of the composite materials in the sky car are carbon fiber, and the remaining about 10 percent are glass fiber. In eVTOL aircraft, carbon fiber is widely used in structural components and propulsion systems, accounting for about 75-80%, while internal applications such as beams, seat structures, etc., account for 12-14%, battery systems, avionics, etc., account for 8-12%.
Leading domestic eVTOL manufacturers, such as Ehang Intelligence, Xiaopeng Hutian, Feng Fei Aviation, etc., have adopted carbon fiber composite materials in their design schemes. For example, XOPeng’s Voyager X2 also uses carbon fiber composite materials for its rotor blades and landing gear. These applications demonstrate the important role of carbon fiber in the low-altitude economy, but also portend a large demand for carbon fiber.
With the gradual liberalization of global policies in the low-altitude field, as well as the continuous emergence of new materials and new processes, the application of carbon fiber in low-altitude aircraft is ushering in unprecedented development opportunities. It is expected that the demand for carbon fiber in a single eVTOL is between 100-400kg, which provides a broad space for the development and upgrading of carbon fiber industry chain related enterprises.
Glass fiber composite material
Glass fiber reinforced plastics (GFRP) play an important role in the manufacture of low-altitude aircraft such as UAVs because of its corrosion resistance, high and low temperature resistance, radiation resistance, flame retardant and anti-aging properties. The application of this material helps to reduce the weight of the aircraft, increase the payload, save energy, and achieve a beautiful appearance design. Therefore, GFRP has become one of the key materials in the low-altitude economy.
In the production process of low-altitude aircraft, glass fiber cloth is widely used in the manufacture of key structural components such as fuselage, wing and tail. Its lightweight characteristics help improve the cruise efficiency of the aircraft and provide greater structural strength and stability.
For components that require excellent wave transmission, such as radomes and fairings, fiberglass composites are commonly used. For example, high-altitude long-endurance UAVs and the U.S. Air Force’s RQ-4 Global Hawk use carbon fiber composite materials for their wings, tails, engine bay and rear fuselage, while the radome and fairing use glass fiber composite materials to ensure clear signal transmission
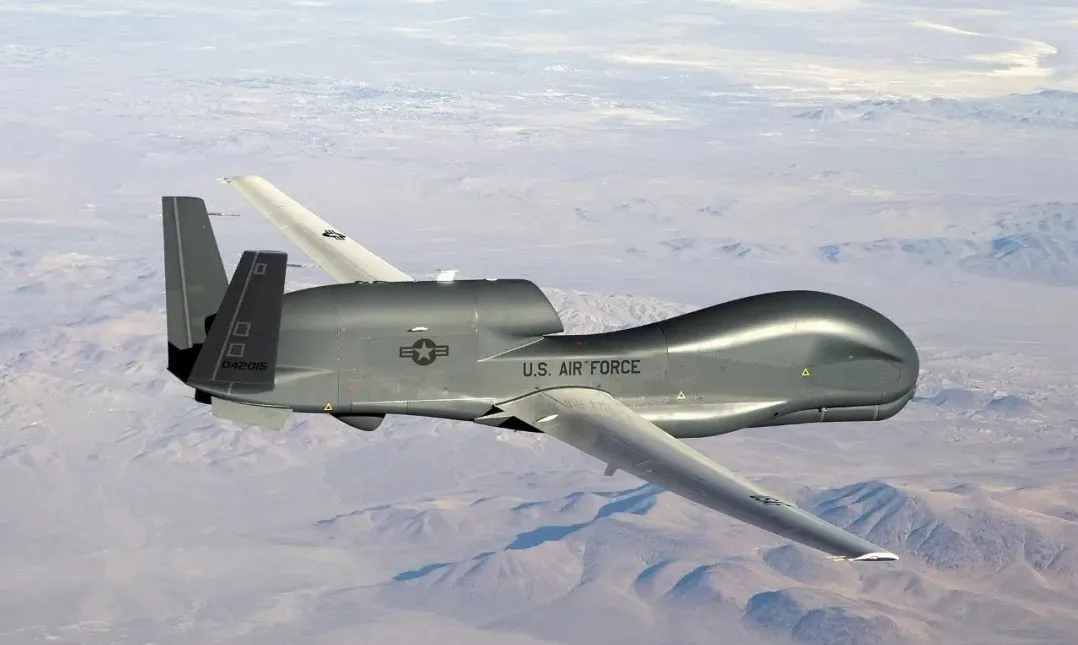
In the aerospace sector, the application of glass fiber is not limited to improving structural performance, it also plays an important role in the exterior design of aircraft.
For example, fiberglass cloth can be used to make fairings and Windows for aircraft, which not only enhances the appearance of the aircraft, but also enhances the comfort of the ride. Similarly, in satellite design, fiberglass cloth can also be used to construct the outer surface structure of solar panels and antennas, thereby improving the appearance and functional reliability of the satellite.
I like this weblog so much, saved to my bookmarks.