In the design and manufacture of carbon fiber composite drones, the adjustment of laying angles and material layers is often used to achieve the requirements for structural elasticity and stiffness distribution. Carbon fiber composite material is one of the most commonly used reinforcement materials in drones. The production of drones using carbon fiber composite materials generally involves the following three molding processes:
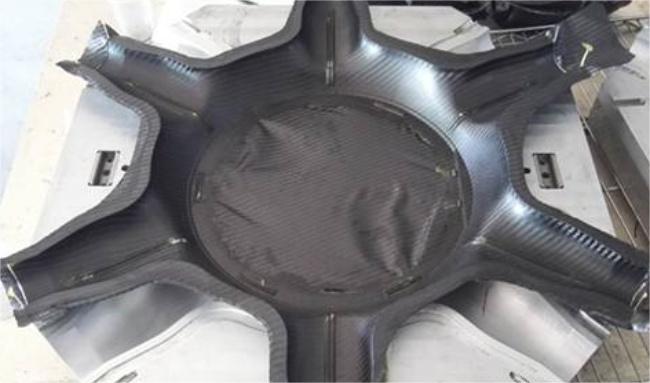
Autoclave Molding Process
Autoclave molding is one of the high-performance molding processes for composite materials. It is often used to manufacture composite components and main load-bearing components of drones with high speed requirements. Carbon fiber composite components molded in an autoclave have good internal quality, uniform resin content, and superior mechanical properties. However, the autoclave molding process also has some disadvantages. This process requires high-end equipment, high initial investment and processing costs, and relatively poor economics. From a cost perspective, low-temperature and low-pressure molding techniques are often chosen as an alternative when budgets are limited. Additionally, during the autoclave molding process of carbon fiber composite materials, phenomena such as resin flow, heat transfer, chemical cross-linking, and void formation can interact and influence each other, which increases the difficulty of process control. Once the control is not accurate, processing defects such as resin deficiency and high porosity may occur. To ensure the quality of carbon fiber composite drone components, Wuxi Zhishang New Material Technology Co., Ltd. simulates the dynamic changes, resin flow, and heat transfer during the autoclave molding process. Based on the model data, the pressure and temperature curves of the autoclave process can be well controlled.
Vacuum Bag Molding Process
Compared to the autoclave process, the vacuum bag molding process is simpler and does not require a high initial investment. The operating difficulty is moderate. However, this molding method has low pressure and is only suitable for composite components with low quality standards. It is mostly used to manufacture honeycomb sandwich structures and laminated structures not exceeding 1.5mm. Due to its cost advantage, this process method is widely used in the manufacture of low-speed drones. Because in the manufacture of small and low-speed drones, vacuum bag molding technology can meet the production requirements of most parts.
In practical operation, since vacuum bag molding requires prepreg laying, wet laying, and other processes, wet operation is easily affected by human factors, which can lead to uneven glue application. This situation is particularly evident in the molding of sandwich structures. Additionally, unreasonable brushing directions can easily lead to bending and changes in fiber directions, threatening the stability of carbon fiber composite parts. Wuxi Zhishang New Material Technology Co., Ltd. uses prepreg laying, which can effectively avoid the above problems and improve the stability of parts.
Compression Molding Process
Compression molding is more suitable for the manufacture of foam sandwich composite components. It combines the advantages of autoclave molding technology and vacuum bag molding. It has high production efficiency, high molding pressure, moderate equipment investment and cost, and good economics. Most parts of the drone’s rudder surface that use foam sandwich structures adopt this molding process. In the manufacture of carbon fiber drone wingboards, the use of compression molding can also ensure the appearance quality and wing shape accuracy of the drone’s wings, improving the overall manufacturing quality of the drone. However, pressure control is the most critical step in this process. Through product structure analysis and long-term experience, Wuxi Zhishang New Material Technology Co., Ltd. can more accurately determine the pressure control parameters to ensure the performance level of structural components.
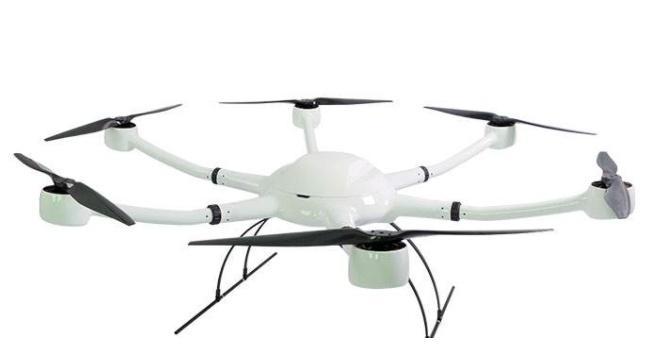
The application of carbon fiber composite materials is an important trend in drone manufacturing and an effective way to meet the requirements of drones in terms of range, flight time, flight altitude, manufacturing cost, and concealment. The structural design and manufacturing process optimization of carbon fiber composite drones are currently the keys to the application of carbon fiber drones. The former requires the efforts of drone designers, while the latter requires continuous experimentation and innovation in the research and development of carbon fiber composite materials. The increasing application of carbon fiber in drones will effectively enhance the manufacturing standards of drones in China.