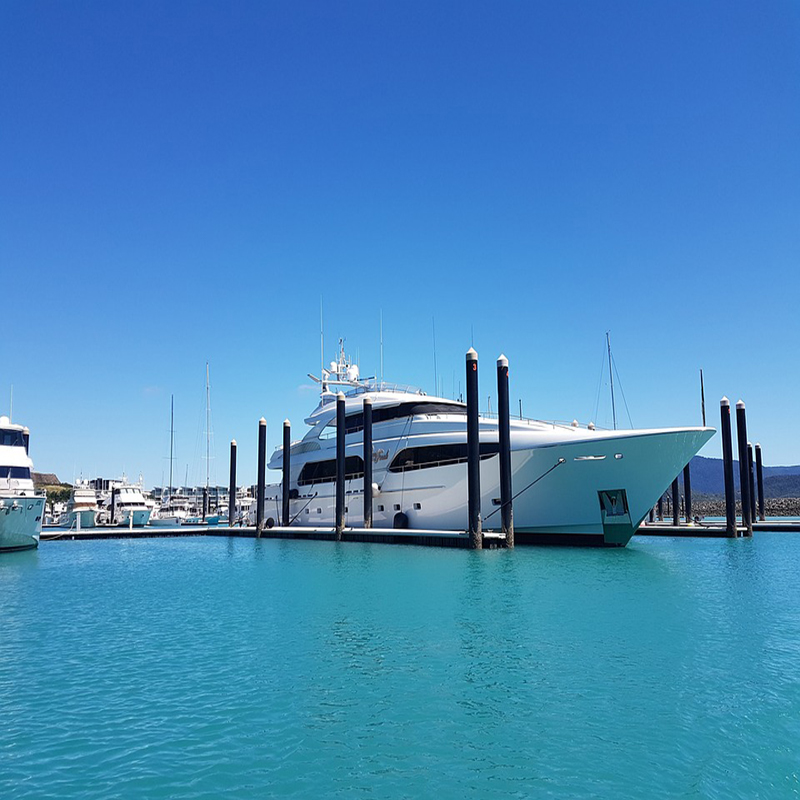
Marine composite materials, especially those applied to the hull structure, are primarily polymer-based composites. They can be divided into two main types based on their structure: laminated composites (fiber-reinforced composites) and sandwich-structured composites. These composites consist of three essential components: reinforcing material, resin (or matrix), and core material.
According to the load-bearing positions, they can be categorized into primary load-bearing structures, secondary load-bearing structures, and non-load-bearing structures. Based on their functions, they can be grouped into five major series: structural, damping, acoustic (including sound absorption, sound insulation, and sound transmission), stealth (including wave absorption, wave transmission, reflection, and frequency selection), and protective materials.
The superior performance of these materials is mainly reflected in: light weight and high strength, which can effectively improve the reserve buoyancy of the hull; integration of structure and function, allowing for performance design while meeting structural load-bearing requirements, often with additional properties such as acoustics, radar, vibration reduction, protection, and low magnetic susceptibility; the general material forming process is also the structural forming process; corrosion resistance, satisfying the demanding marine environment requirements of high salinity, high humidity, and ultraviolet radiation; and aging resistance, satisfying the long-life requirements of ships.
At present, carbon fiber composite materials have been widely used in aerospace, sports and leisure, automotive industry, environmental energy, civil engineering, and other fields, and their application range is almost ubiquitous. Among them, progress is being made in the application of carbon fiber in small boats, yachts, large ships, and other shipping areas. Carbon fiber is an ideal material for the shipping industry because it can reduce hull vibration and maintain a good wireless communication environment between ships.
In addition, the most important reason for using carbon fiber is that this material can improve ship speed and fuel economy by reducing weight. For example, by completely replacing glass fiber composite materials (GFRP) with carbon fiber reinforced composite materials (CFRP), the weight of the hull can be reduced to 30% of the original.
The application of carbon fiber and its composite materials in yachts can further reduce weight and improve the stability of the ship by using CFRP in the superstructure and deck equipment. Carbon fiber transmission shafts can also achieve weight reduction and vibration reduction. Carbon fiber also has potential applications in propeller blades.
In the 1940s, the US Navy used composite materials to build small ships, thus opening a new chapter in shipbuilding. In the mid-1950s, it stipulated that ships below 16 meters must be made of composite materials. With the development of material science, the improvement of construction methods and application forms, in 1994, the United States used composite materials to build the “Avenger” class minesweeper with a length of 68.3 meters. The deep-diving submarine built in 1996 used graphite fiber reinforced composite materials for its hull, which could dive to a depth of 6096 meters. The “Stiletto” (M80), a new type of high-speed stealth experimental speedboat manufactured in 2006, is the largest hull made of carbon fiber in one molding. Due to the absence of welding and riveting in the process, the overall lightweight of the ship is greatly achieved. With a length of 24.4 meters, a width of 12.2 meters, and a draught of only 0.9 meters, the displacement is 67 tons, allowing the speedboat to easily achieve high speeds. The Los Angeles-class nuclear submarine of the US Navy also uses new composite materials to manufacture sonar domes, which are 7.6 meters long, with a maximum diameter of 8.1 meters, and have excellent performance. The US Navy is also developing military ships into traditional hovercraft. Conventional hovercraft use aluminum hard shells similar to those on aircraft as base materials, while the US All-Terrain Amphibious Hovercraft Company (ATLAS Hovercraft) has developed a fully composite hovercraft called the AH-100-P, which can accommodate 150 passengers.
As a major manufacturer of composite material ships in Asia, Japan began building glass steel ships in 1953. By the 1970s, Japanese fishing boats began to widely use glass steel. Since then, Japan has manufactured tens of thousands of glass steel fishing boats every year, and the technology has become increasingly sophisticated. Nowadays, Japan’s glass steel production has jumped to second in the world, with 76.3% of the glass steel used in marine motorized fishing boats. At the same time, Japan also occupies an important position in the international arena in the development and production of high-performance composite materials such as carbon fiber. Its high-performance ships, racing boats, and luxury yachts are now widely using high-performance carbon fiber composite materials.
Carbon fiber has two types: high strength and high modulus, with characteristics of high stiffness, high yield strength, and high bending strength. It is generally used in the manufacture of high-performance, high-speed ships. Japanese carbon fiber is sold worldwide, mainly used in the manufacture of high-speed speedboats, high-performance racing boats, luxury yachts, and other boats.
Aramid fibers have the characteristics of high specific strength, high toughness, impact resistance, and bulletproofness, and are used in ship components that require high tensile, dynamic loads, and bulletproof requirements. Due to their low compressive and bending strength, they are not suitable for the manufacture of high-compression, high-bending hulls, and are only suitable for ships with strict weight restrictions.
In shipbuilding, when considering costs, a design method using hybrid fiber composite materials has emerged under the premise of meeting design requirements. The hybrid use of multiple fiber-reinforced materials overcomes some of the shortcomings of single-fiber composite materials, improves physical and mechanical properties, and further enhances the designability of the materials. Two-dimensional and three-dimensional fabrics formed by reinforced materials can be manufactured according to design needs, satisfying the strength, intra-layer, and inter-layer performance requirements of warships, and further achieving lightweight and high-strength requirements for warships.
Due to the lightweight nature of composite materials, the US Navy plans to use glass-reinforced phenolic composite materials in power pods, including cylinders, cylinder heads, oil pans, cam covers, support rollers, speed control sprockets, water pumps, oil pumps, tackle blocks, etc. for marine diesel engines.
Some mechanical components of surface combatants can also be manufactured using composite materials. Amid the trend of reducing the weight of ship hulls, reducing the weight of power transmission components in the propulsion system has also been put on the agenda. A typical example is high-speed ships driven by 2 or 4 high-speed diesel engines through reduction gearboxes to drive waterjet propellers. The distances between the diesel engines and gearboxes, as well as between the gearboxes and waterjet propulsion devices, have been shortened. In particular, the narrow space of a catamaran requires the staggered arrangement of 4 diesel engines, and the power generated by the front diesel engine must be transmitted through the rear diesel engine. Therefore, this requires the installation of the lightest transmission device with the fewest components. The use of CFRP (carbon fiber reinforced plastic) drive shafts can easily achieve the purpose of reducing the weight of transmission components. The main advantages of CFRP drive shafts include: significantly reduced weight; high critical speed, usually without the need for bearings on long shaft systems, reducing the number of bearings, lowering costs, lightening the shaft system, reducing components, saving on bearing support costs, and reducing weight; corrosion resistance, low magnetic signals, electrical signals, wear resistance, and reducing structural and airborne noise up to 520 dB.